- Industrial sector, Mining sector -
Manufacturing of Steel Supports for Hamilton Wheels
Home > Realisations > Manufacturing of Steel Supports for Hamilton Wheels
Over the past few weeks, our company has completed a project involving the manufacturing of mechanical components crucial for the proper operation of an industrial rotary furnace: supports for Hamilton wheels.
Here are a few photos and a summary of this project.
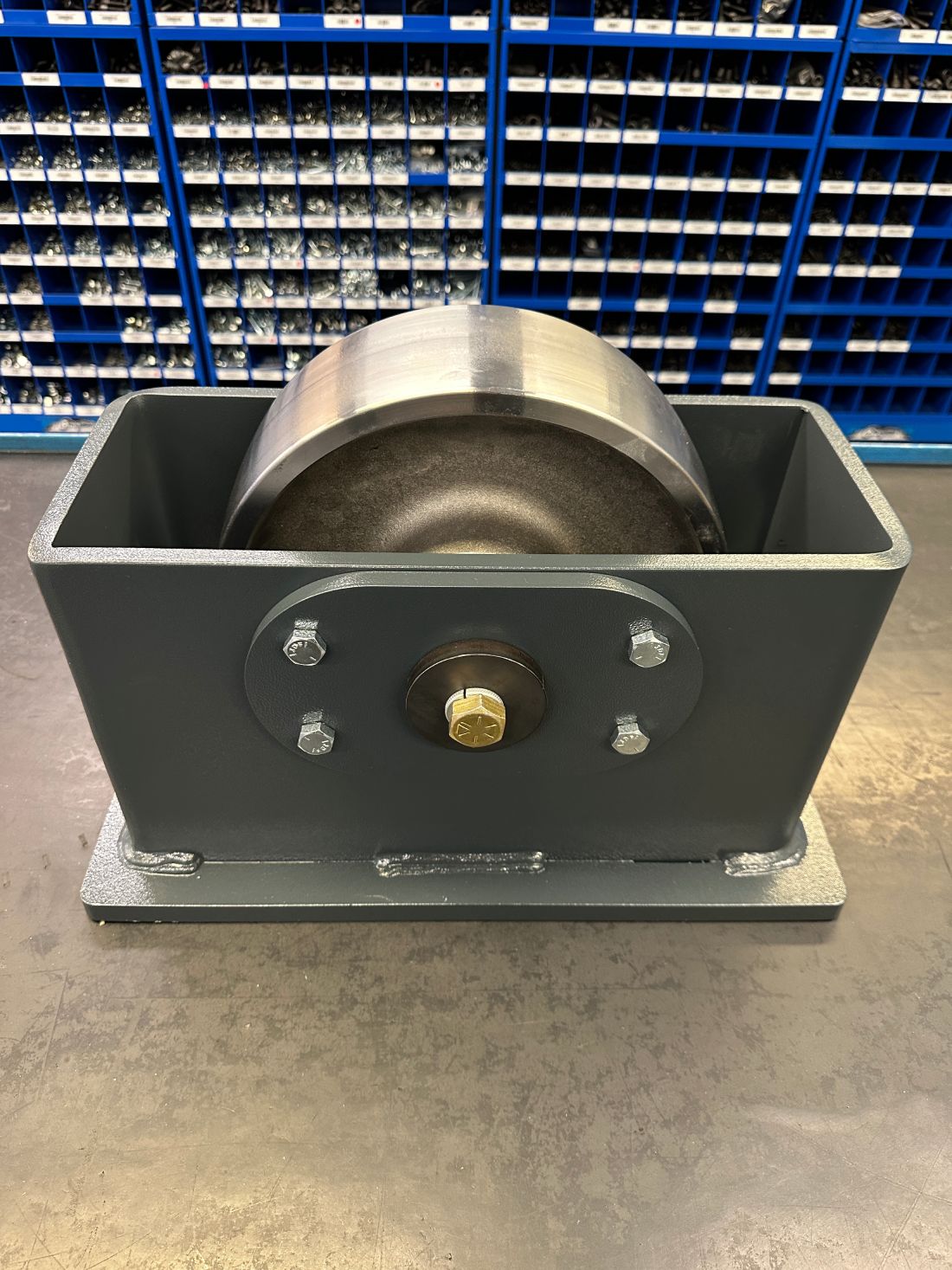
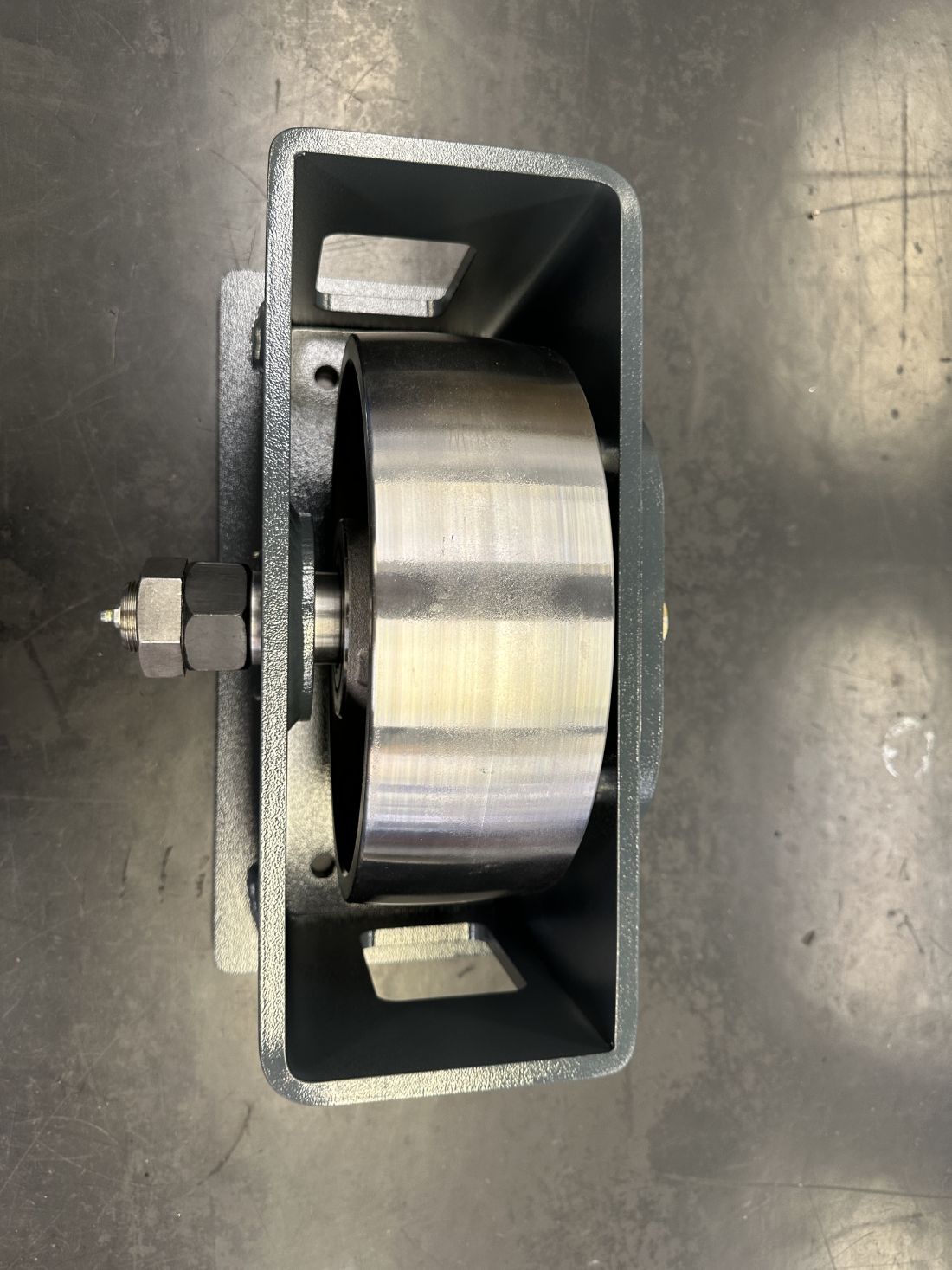
A Project Our Team Had Already Completed for the Same Client
This isn’t the first time that Magotteaux, a company specializing in ball mill grinding media, has entrusted us with a project to manufacture supports for Hamilton casters.
In fact, they had previously commissioned us to create metallic bases for wheels, requiring the fabrication of 24 bases.
Pleased with the outcome, they have commissioned us once again. This time, the order was for the same product, but only in two units, intended as spare bases in case of breakage.
What is a Hamilton Wheel?
Hamilton wheels and casters are commonly used in various applications such as conveyors systems, carts, and industrial machinery. They are renowned for their durability and quality.
The Crucial Role of Hamilton Wheel Supports at the Client’s Facility
In the client’s facility, Hamilton casters are installed under a massive rotary furnace weighing nearly 250,000 pounds, highlighting the need for exceptionally sturdy bases!
This furnace is used during the metal heating stage for processing mill grinding balls.
That’s why these wheels and their respective supports are of paramount importance, as without them, it would be impossible to ensure the rotation of the metal furnace used for the thermal treatment of metal balls.
A Project That Brought Together Various Departments
In order to carry out this mandate brilliantly, several of our departments got their hands dirty.
Leading the effort, our Mechanical Engineering Department took on the task of crafting the wheel base designs. These are Omnifab-signed designs, from start to finish.
Following this initial step, the project saw the involvement of laser cutting, metal bending, welding, machining, and mechanical departments, each playing a pivotal role. In the machining phase, our skilled machinists utilized our CNC machining center, followed by crafting the shaft on a conventional lathe. A bit of milling was also performed to achieve the final result.
The Importance of Material Selection and Surface Treatment
To construct something exceptionally strong and durable, we chose 44W steel for the bases. This steel is known for having the perfect characteristics for this project.
Then, for the shaft, we also selected steel, but opted for 1020 steel, which is better suited for this part.
Finally, with the aim of further increasing the component’s longevity, we subjected the washer to a black oxide treatment.
Do you need spare parts?
Constraints for This Project
Hamilton wheels are not manufactured at Omnifab. They must be ordered, and sometimes, it can take up to six weeks before we receive them. Obviously, these delays are beyond our control, but they still impact the delivery of the order.
As for the manufacturing process, careful attention was needed to ensure the proper fit of the shaft’s bushings since they pass through a very, very narrow space.
Our Specialty: Ensuring Timely Delivery of Your Parts!
In conclusion, the delivery timeline for the wheel surpassed our initial estimates. As a result, we were able to complete this project from inception to completion within just three weeks.
Moreover, we always keep the drawings and specifications of our projects, enabling us to expedite future deliveries if the client requires the same component again. Thus, Magotteaux can count on us for the rapid provision of new supports when tight deadlines arise.