- Food sector, Industrial sector, Sorting Centres -
Design and manufacturing of a custom conveyor for an assembly line
Home > Realisations > Design and manufacturing of a custom conveyor for an assembly line
In the past year, we had the opportunity to undertake a highly intriguing industrial mechanical manufacturing mandate: designing, manufacturing, and installing a custom conveyor in a factory producing small recreational watercraft.
Here’s a summary of this project that required the involvement of all our departments.
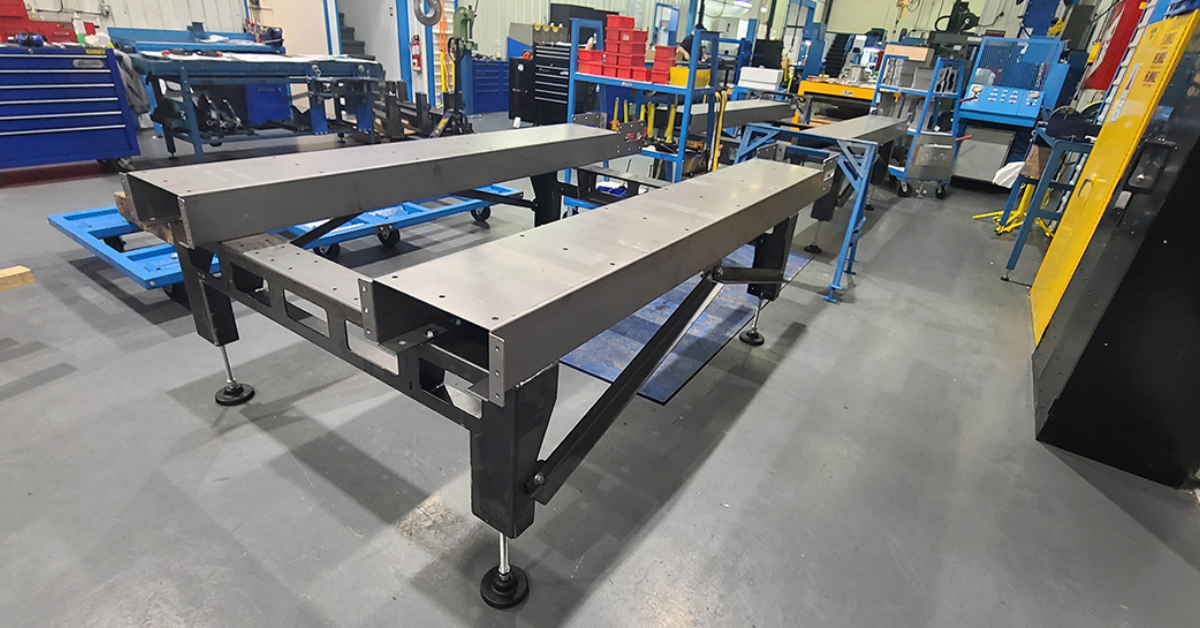
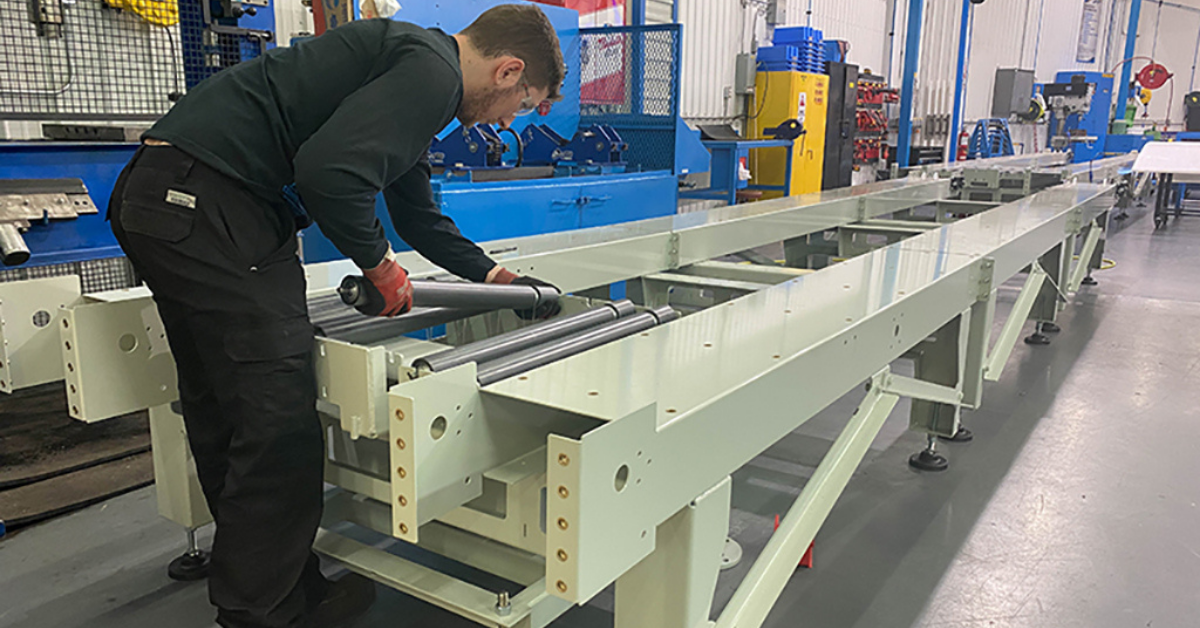
Our mission: replace an old conveyor ill-suited to the factory workforce’s needs
When the client approached us, they were looking to modernize their assembly line to make it more efficient, ergonomic, and safe.
The biggest issue was that when installing fixtures on the product (fishing rod holders, padded seats, etc.), their employees had to lift and handle these items over a certain distance.
What’s more, the employees struggled to find a comfortable working position to perform their tasks. All of this posed a risk of work-related accidents and illnesses, as well as slowing down the production pace.
Our solution: a custom-made conveyor that adapts to each worker’s morphology
Once we had a clear understanding of the client’s specific needs, our team of designers began brainstorming a solution that not only would make the employees’ work safer and less physically demanding but also would boost production efficiency.
The solution we presented to the client was a custom conveyor connecting all workstations and featuring height settings that the workers could easily adjust.
Forget standard conveyors and choose our 100% customized systems
Features that enhance production line ergonomics
To ensure easy movement from one workstation to another, a gravity-powered (non-motorized) roller conveyor was the best choice. With a simple push, employees could move the product to the next workstation. No more heavy lifting required.
Additionally, our designers and mechanical engineers wanted to make sure that at each workstation, the height of the conveyor section could be adjusted using a foot pedal. This way, employees of all builds could enjoy a workstation suited to their stature.
Safety was also a top priority during the conveyor’s design
Creating this type of conveyor also led us to perform a risk analysis to ensure that all potential hazards were controlled and that this new equipment met the highest safety standards.
For instance, the new conveyor would have no pinch points, sharp corners, or rough surfaces.
After design phase, it was time to manufacture the conveyor
After going through the hands of our engineers and industrial designers, the final concept, approved by the client, was ready to move into the manufacturing phase. Needless to say, creating such an elaborate conveyor required the contribution of several of our departments.
Without going into too many details, it’s worth mentioning that our machining and welding teams manufactured various parts of the conveyor. To achieve precisely dimensioned parts and the desired finish, various processes such as laser cutting and electrostatic painting were used.
Then, our industrial mechanics team assembled multiple sections of the conveyor. They were also responsible for installing the mechanical, hydraulic, and electrical components that allowed for workstation height adjustments.
Final step: delivery and installation of the conveyor at the client’s site
Quite obviously, a conveyor that runs through a large part of a factory cannot be completely assembled before being delivered.
As a result, some of our employees traveled to the client’s facility to complete the assembly, installation, and calibration of the conveyor.
To optimize your production line, trust Omnifab!
For us, this achievement is proof that Omnifab has all the expertise required to optimize a production line or industrial machine, whether it’s in terms of efficiency, ergonomics, or safety.
Not to mention that our turnkey approach reduces lead times and intermediaries. Just let us know your business objectives, and we’ll come up with a solution, put it into design, manufacture it, and install it for you. We take care of everything, as promised!
So, if you want to take your company to the next level, contact us!